- 在工廠精益布局規(guī)劃中,系統(tǒng)布置設(shè)計(jì)SLP該如何應(yīng)用?
- 精益生產(chǎn)的起源及發(fā)展史?
- 戴爾的精益生產(chǎn)與豐田生產(chǎn)模式有哪些相同點(diǎn)與不同點(diǎn)
- 精益"準(zhǔn)時(shí)化"生產(chǎn)方式的概念,基本原則及特點(diǎn)是什么?
精益生產(chǎn)(LeanProduction)又稱精良生產(chǎn),其中“精”表示精良、精確、精美;“益”表示利益、效益等等。精益生產(chǎn)就是及時(shí)制造,消滅故障,消除一切浪費(fèi),向零缺陷、零庫(kù)存進(jìn)軍。它是美國(guó)麻省理工學(xué)院在一項(xiàng)名為“國(guó)際汽車***”的研究項(xiàng)目中提出來的。它們?cè)谧隽舜罅康恼{(diào)查和對(duì)比后,認(rèn)為日本豐田汽車公司的生產(chǎn)方式是最適用于現(xiàn)代制造企業(yè)的一種生產(chǎn)組織管理方式,稱之為精益生產(chǎn),以針對(duì)美國(guó)大量生產(chǎn)方式過于臃腫的弊病。精益生產(chǎn)綜合了大量生產(chǎn)與單件生產(chǎn)方式的優(yōu)點(diǎn),力求在大量生產(chǎn)中實(shí)現(xiàn)多品種和高質(zhì)量產(chǎn)品的低成本生產(chǎn)。
與大量生產(chǎn)方式相比,日本所***用的精益生產(chǎn)方式的優(yōu)越性主要表現(xiàn)在以下幾個(gè)方面:
1、所需人力***--無論是在產(chǎn)品開發(fā)、生產(chǎn)系統(tǒng),還是工廠的其他部門,與大量生產(chǎn)方式下的工廠相比,最低能減至1/2;
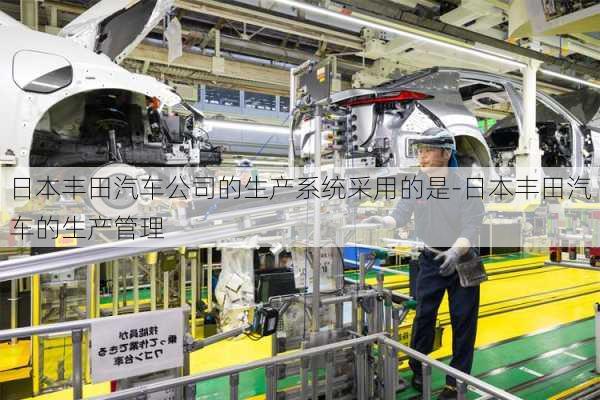
2、新產(chǎn)品開發(fā)周期—最低可減至l/2或2/3;
3、生產(chǎn)過程的在制品庫(kù)存—最低可減至大量生產(chǎn)方式下一般水平的1/10;
4、工廠占用空間—最低可減至***用大量生產(chǎn)方式下的1/2;
5、成品庫(kù)存—最低可減至大量生產(chǎn)方式下平均庫(kù)存水平的1/4;
精益生產(chǎn)方式是徹底地追求生產(chǎn)的合理性、高效性,能夠靈活地生產(chǎn)適應(yīng)各種需求的高質(zhì)量產(chǎn)品的生產(chǎn)技術(shù)和管理技術(shù),其基本原理和諸多方法,對(duì)制造業(yè)具有積極的意義。精益生產(chǎn)的核心,即關(guān)于生產(chǎn)***和控制以及庫(kù)存管理的基本思想,對(duì)豐富和發(fā)展現(xiàn)代生產(chǎn)管理理論也具有重要的作用。
精益生產(chǎn)的特點(diǎn):
1、拉動(dòng)式準(zhǔn)時(shí)化生產(chǎn)
以最終用戶的需求為生產(chǎn)起點(diǎn).強(qiáng)調(diào)物流平衡,追求零庫(kù)存,要求上一道工序加工完的零件立即可以進(jìn)入下一道工序。
組織生產(chǎn)線依靠一種稱為看板(Kanban)的形式。即由看板傳遞下道向上道需求的信息(看板的形式不限,關(guān)鍵在于能夠傳遞信息)。生產(chǎn)中的節(jié)拍可由人工干預(yù)、控制,但重在保證生產(chǎn)中的物流平衡(對(duì)于每一道工序來說,即為保證對(duì)后退工序供應(yīng)的準(zhǔn)時(shí)化)。由于***用拉動(dòng)式生產(chǎn),生產(chǎn)中的***與調(diào)度實(shí)質(zhì)上是由各個(gè)生產(chǎn)單元自己完成,在形式上不***用集中***,但操作過程中生產(chǎn)單元之間的協(xié)調(diào)則極為必要。
2、全面質(zhì)量管理
強(qiáng)調(diào)質(zhì)量是生產(chǎn)出來而非檢驗(yàn)出來的,由生產(chǎn)中的質(zhì)量管理來保證最終質(zhì)量.生產(chǎn)過程中對(duì)質(zhì)量的檢驗(yàn)與控制在每一道工序都進(jìn)行。重在培養(yǎng)每位員工的質(zhì)量意識(shí),在每一道工序進(jìn)行時(shí)注意質(zhì)量的檢測(cè)與控制,保證及時(shí)發(fā)現(xiàn)質(zhì)量問題.如果在生產(chǎn)過程中發(fā)現(xiàn)質(zhì)量問題,根據(jù)情況,可以立即停止生產(chǎn),直至解決問題,從而保證不出現(xiàn)對(duì)不合格品的無效加工。
對(duì)于出現(xiàn)的質(zhì)量問題,一般是組織相關(guān)的技術(shù)與生產(chǎn)人員作為一個(gè)小組,一起協(xié)作,盡快解決。
3、團(tuán)隊(duì)工作法
團(tuán)隊(duì)工作法(Teamwork)。每位員工在工作中不僅是執(zhí)行上級(jí)的命令。更重要的是積極地參與,起到?jīng)Q策與***決策的作用.組織團(tuán)隊(duì)的原則并不完全按行政組織來劃分,而主要根據(jù)業(yè)務(wù)的關(guān)系來劃分。團(tuán)隊(duì)成員強(qiáng)調(diào)一專多能,要求能夠比較熟悉團(tuán)隊(duì)內(nèi)其他工作人員的工作,保證工作協(xié)調(diào)的順利進(jìn)行。團(tuán)隊(duì)人員工作業(yè)績(jī)的評(píng)定受團(tuán)隊(duì)內(nèi)部的評(píng)價(jià)的影響。(這與日本獨(dú)特的人事制度關(guān)系較大)團(tuán)隊(duì)工作的基本氛圍是信任,以一種長(zhǎng)期的監(jiān)督控制為主,而避免對(duì)每一步工作的稽核,提高工作效率。團(tuán)隊(duì)的組織是變動(dòng)的,針對(duì)不同的事物,建立不同的團(tuán)隊(duì),同一個(gè)人可能屬于不同的團(tuán)隊(duì)。
4、并行工程
并行工程(ConcurrentEngineering)。在產(chǎn)品的設(shè)計(jì)開發(fā)期間,將概念設(shè)計(jì)、結(jié)構(gòu)設(shè)計(jì)、工藝設(shè)計(jì)、最終需求等結(jié)合起來,保證以最快的速度按要求的質(zhì)量完成。各項(xiàng)工作由與此相關(guān)的項(xiàng)目小組完成。進(jìn)程中小組成員各自安排自身的工作,但可以定期或隨時(shí)反饋信息并對(duì)出現(xiàn)的問題協(xié)調(diào)解決。依據(jù)適當(dāng)?shù)男畔⑾到y(tǒng)工具,反饋與協(xié)調(diào)整個(gè)項(xiàng)目的進(jìn)行。利用現(xiàn)代CIM技術(shù),在產(chǎn)品的研制與開發(fā)期間,***項(xiàng)目進(jìn)程的并行化。
在工廠精益布局規(guī)劃中,系統(tǒng)布置設(shè)計(jì)SLP該如何應(yīng)用?
豐田UPS條件是指豐田汽車公司在其生產(chǎn)過程中所要求的一系列標(biāo)準(zhǔn)和條件。UPS是豐田生產(chǎn)系統(tǒng)(Toyota Production System)的一部分,它是豐田汽車公司成功的關(guān)鍵之一。這一生產(chǎn)系統(tǒng)的核心理念是通過精益生產(chǎn)、減少浪費(fèi)和持續(xù)改進(jìn)來實(shí)現(xiàn)高效率和高質(zhì)量的汽車生產(chǎn)。
豐田UPS條件包括以下幾個(gè)方面:
1. 精益生產(chǎn):豐田UPS要求實(shí)現(xiàn)精益生產(chǎn),即通過消除浪費(fèi)、提高效率和質(zhì)量來實(shí)現(xiàn)生產(chǎn)過程的優(yōu)化。這包括精確***、及時(shí)交付、減少庫(kù)存、降低成本等方面。
2. 持續(xù)改進(jìn):豐田UPS強(qiáng)調(diào)持續(xù)改進(jìn),即通過員工的參與和持續(xù)的改進(jìn)活動(dòng)來不斷提高生產(chǎn)過程和產(chǎn)品質(zhì)量。這包括流程改善、問題解決、標(biāo)準(zhǔn)化工作等。
3. 質(zhì)量管理:豐田UPS要求高品質(zhì)的產(chǎn)品,通過嚴(yán)格的質(zhì)量管理和檢驗(yàn)來確保產(chǎn)品符合標(biāo)準(zhǔn)。這包括零缺陷的目標(biāo)、質(zhì)量控制、故障排除等。
4. 人員培訓(xùn)和發(fā)展:豐田UPS注重員工的培訓(xùn)和發(fā)展,通過提供適當(dāng)?shù)呐嘤?xùn)和提升機(jī)會(huì),使員工具備必要的技能和知識(shí),以支持生產(chǎn)系統(tǒng)的順利運(yùn)行。
這些UPS條件的目的是為了確保豐田汽車生產(chǎn)的高效率、高質(zhì)量和可持續(xù)發(fā)展。通過遵循這些條件,豐田汽車公司能夠?qū)崿F(xiàn)持續(xù)改進(jìn)和不斷提高客戶滿意度,成為全球領(lǐng)先的汽車制造商之一。
拓展內(nèi)容:豐田UPS條件的實(shí)施也得益于豐田公司的企業(yè)文化,其中包括“精益求精”、“尊重人”的價(jià)值觀。豐田公司注重員工的參與和團(tuán)隊(duì)合作,鼓勵(lì)員工提出改進(jìn)建議和解決問題,以推動(dòng)生產(chǎn)系統(tǒng)的不斷完善。此外,豐田UPS條件的成功實(shí)施還得益于供應(yīng)鏈的協(xié)同和合作,以確保原材料和零部件的及時(shí)供應(yīng),以支持生產(chǎn)過程的順利進(jìn)行??傊?,豐田UPS條件的意義在于通過優(yōu)化生產(chǎn)系統(tǒng)和提高產(chǎn)品質(zhì)量,實(shí)現(xiàn)持續(xù)的競(jìng)爭(zhēng)優(yōu)勢(shì)和顧客滿意度。
精益生產(chǎn)的起源及發(fā)展史?
轉(zhuǎn)載以下資料供參考 精益生產(chǎn)工具,謝謝! 1、6S與目視控制 “6S”是整理(Seiri) 、整頓(Seiton) 、清掃(Seiso) 、清潔(Seikeetsu)和素養(yǎng)(Shitsuke)、安全(safety)這6個(gè)詞的縮寫 ”6S” ,起源于日本。6S是創(chuàng)建和保持組織化,整潔和高效工作場(chǎng)地的過程和方法,可以教育、啟發(fā)和養(yǎng)成良好“人性”習(xí)慣,目視管理可以在瞬間識(shí)別正常和異常狀態(tài),又能快速、正確的傳遞訊息。兩天的課程可以幫助學(xué)員: · 了解為什么要做6S,掌握推行6S和目視管理的步驟和方法 ; · 了解視覺控制工具的類型,學(xué)會(huì)如何創(chuàng)建視覺控制工具以及一些最基本的可以快速改進(jìn)所有工作區(qū)域的新工具?!?、準(zhǔn)時(shí)化生產(chǎn)(JIT) 準(zhǔn)時(shí)生產(chǎn)方式是起源于日本豐田汽車公司,其基本思想是“只在需要的時(shí)候,按需要的量生產(chǎn)所需的產(chǎn)品” 。這種生產(chǎn)方式的核心是追求一種無庫(kù)存的生產(chǎn)系統(tǒng),或使庫(kù)存達(dá)到最小的生產(chǎn)系統(tǒng)。通過本課程的學(xué)習(xí),使學(xué)員能夠: · 認(rèn)識(shí)增值與非增值活動(dòng),減少或消除非增值和浪費(fèi) ; · 七種浪費(fèi)的識(shí)別以及最終消除浪費(fèi); · 學(xué)會(huì)運(yùn)用各種拉動(dòng)方式實(shí)現(xiàn)準(zhǔn)時(shí)化生產(chǎn)。 3、看板管理( Kanban ) Kanban是個(gè)日語名詞,表示一種掛在或貼在容器上或一批零件上的標(biāo)簽或卡片,或流水線上各種顏色的信號(hào)燈、電視圖象等。看板是可以作為交流廠內(nèi)生產(chǎn)管理信息的手段??窗蹇ㄆ喈?dāng)多的信息并且可以反復(fù)使用。常用的看板有兩種:生產(chǎn)看板和運(yùn)送看板 。本課程將使學(xué)員能夠: · 介紹拉動(dòng)系統(tǒng)看板以及用于管理過程的目視化看板,以及這些看板對(duì)于生產(chǎn)組織,標(biāo)準(zhǔn)化作業(yè)以及持續(xù)改善的重要意義;; · 生產(chǎn)看板的作用就是購(gòu)買的“資金”,你需要關(guān)注的是生產(chǎn)過程中你要“購(gòu)”什么,什么時(shí)候買,買多少?!?、零庫(kù)存管理 工廠的庫(kù)存 管理是供應(yīng)鏈的一環(huán),也是最基本的一環(huán)。就制造業(yè)而言,加強(qiáng)庫(kù)存管理,可縮短并逐步消除原材料、半成品、成品的滯留時(shí)間,減少無效作業(yè)和等待時(shí)間,防止缺貨,提高客戶對(duì) “ 質(zhì)量、成本、交期 ” 三大要素的滿意度。通過兩天的學(xué)習(xí),讓參加學(xué)員能夠: · 了解庫(kù)存管理的基本概念,掌握庫(kù)存分析的方法,學(xué)會(huì)選擇合適的庫(kù)存系統(tǒng); · 學(xué)習(xí)、掌握管理庫(kù)存作業(yè)的技能; · 掌握庫(kù)存作業(yè)管理表單、程序的制作與實(shí)施技巧?!?、全面生產(chǎn)維護(hù)( TPM ) TPM起源于日本, 是以全員參與的方式,創(chuàng)建設(shè)計(jì)優(yōu)良的設(shè)備系統(tǒng),提高現(xiàn)有設(shè)備的利用率,實(shí)現(xiàn)安全性和高質(zhì)量,防止故障發(fā)生,從而使企業(yè)達(dá)到降低成本和全面生產(chǎn)效率的提高。我們希望學(xué)員通過此次課程: · 理解5S與TPM 的關(guān)系; · 掌握OEE的計(jì)算和如何改善OEE; · 掌握實(shí)施TPM 的方法 ; · 如何建立和維護(hù)設(shè)備的歷史記錄,評(píng)價(jià)目前的TPM 水平?!?、運(yùn)用價(jià)值流圖來識(shí)別浪費(fèi) 生產(chǎn)過程中到處充斥著驚人的浪費(fèi)現(xiàn)象,價(jià)值流圖(Value Stream M***ing)是實(shí)施精益系統(tǒng)、消除過程浪費(fèi)的基礎(chǔ)與關(guān)鍵點(diǎn)。通過 本課程的學(xué)習(xí),可使學(xué)員: · 發(fā)現(xiàn)過程中何處產(chǎn)生浪費(fèi) , 識(shí)別精益的改進(jìn)機(jī)會(huì); · 認(rèn)識(shí)價(jià)值流的構(gòu)成因素與重要性; · 掌握實(shí)際繪制“價(jià)值流圖”的能力; · 認(rèn)識(shí)數(shù)據(jù)在價(jià)值流圖示中的應(yīng)用,通過數(shù)據(jù)量化改善機(jī)會(huì)的次序。 7、生產(chǎn)線平衡設(shè)計(jì) 由于流水線布局不合理導(dǎo)致生產(chǎn)工人無謂地移動(dòng),從而降低生產(chǎn)效率;由于動(dòng)作安排不合理、工藝路線不合理,導(dǎo)致工人三番五次地拿起或放下工件。通過本課程的學(xué)習(xí),我們將了解到: · 能夠設(shè)計(jì)和實(shí)施一個(gè)線平衡的生產(chǎn)線 ; · 了解典型流程環(huán)境中的問題及如何影響那些問題 ; · 知道何時(shí)使生產(chǎn)率最大化?!?、拉系統(tǒng)與補(bǔ)充拉系統(tǒng) 所謂拉動(dòng)生產(chǎn)是以看板管理為手段,***用“取料制”即后道工序根據(jù)“市場(chǎng)”需要進(jìn)行生產(chǎn),對(duì)本工序在制品短缺的量從前道工序取相同的在制品量,從而形成全過程的拉動(dòng)控制系統(tǒng),絕不多生產(chǎn)一件產(chǎn)品 。 JIT需要以拉動(dòng)生產(chǎn)為基礎(chǔ),而 拉系統(tǒng)操作是精益生產(chǎn)的典型特征。精益追求的零庫(kù)存,主要通過拉系統(tǒng)的作業(yè)方式實(shí)現(xiàn)的。通過本課程的學(xué)習(xí),學(xué)員可以: · 理解拉系統(tǒng)和補(bǔ)充拉系統(tǒng)的定義 ; · 理解拉系統(tǒng)的關(guān)鍵參數(shù)及計(jì)算方法 ; · 如何在多變的環(huán)境中將拉系統(tǒng)應(yīng)用于精益項(xiàng)目 ; · 了解制造拉系統(tǒng)和***購(gòu)拉系統(tǒng)的區(qū)別?!?、降低設(shè)置時(shí)間 (Setup Reduction) 為了使停線等待浪費(fèi)減為最少,縮短設(shè)置時(shí)間的過程就是逐步去除和減少所有的非增值作業(yè),并將其轉(zhuǎn)變?yōu)榉峭>€時(shí)間完成的過程。 精益生產(chǎn)是通過不斷消除浪費(fèi)、降低庫(kù)存、減少不良、縮短制造周期時(shí)間等具體要求來實(shí)現(xiàn)的,降低設(shè)置時(shí)間是幫助我們達(dá)到這一目標(biāo)的關(guān)鍵手法之一。通過本課程的學(xué)習(xí),我們將了解到: · 理解設(shè)置時(shí)間是如何影響流程的周轉(zhuǎn)效率 ; · 學(xué)習(xí)降低設(shè)置時(shí)間的 4 大步驟 ; · 理解為了降低設(shè)置時(shí)間的必須準(zhǔn)備工作?!?0、單件流 JIT是精益生產(chǎn)的終極目標(biāo),它是通過不斷消除浪費(fèi)、降低庫(kù)存、減少不良、縮短制造周期時(shí)間等具體要求來實(shí)現(xiàn)的。單件流是幫助我們達(dá)到這一目標(biāo)的關(guān)鍵手法之一。通過本課程的學(xué)習(xí),我們將了解到: · 單件流與傳統(tǒng)作業(yè)的根本差異 ; · 設(shè)計(jì)如何實(shí)現(xiàn)單件流 ; 通過單件流,您企業(yè)將得到如下益處: ※ 不良狀況明顯顯露,及時(shí)解決 ; ※ 形成團(tuán)隊(duì)驅(qū)動(dòng),作業(yè)人員集中精力 ; ※ 縮短解決問題的時(shí)間 ; ※ 作業(yè)人員作業(yè)時(shí)間增加,***時(shí)間減少 ; ※ 縮小生產(chǎn)面積物流搬運(yùn)減少生產(chǎn)效率提高 。 11、持續(xù)改善 (Kaizen) Kaizen是個(gè)日語名詞,相當(dāng)于CIP。當(dāng)開始精確地確定價(jià)值,識(shí)別價(jià)值流,使為特定產(chǎn)品創(chuàng)造的價(jià)值的各個(gè)步驟連續(xù)流動(dòng)起來,并讓客戶從企業(yè)[2]拉動(dòng)價(jià)值時(shí),奇跡就開始出現(xiàn)了。本課程將使學(xué)員: · 何時(shí)需要改善( Kaizen ),如何應(yīng)用改善( Kaizen ); · 改善( Kaizen )的策略,常用工具和技巧?! 【嫔a(chǎn)實(shí)施步驟 1、選擇要改進(jìn)的關(guān)鍵流程 精益生產(chǎn)方式不是一蹴而就的,它強(qiáng)調(diào)持續(xù)的改進(jìn)。首先應(yīng)該先選擇關(guān)鍵的流程,力爭(zhēng)把它建立成一條樣板線?!?、畫出價(jià)值流程圖 價(jià)值流程圖是一種用來描述物流和信息流的方法。在繪制完目前狀態(tài)的價(jià)值流程圖后,可以描繪出一個(gè)精益遠(yuǎn)景圖(Future Lean Vision)。在這個(gè)過程中,更多的圖標(biāo)用來表示連續(xù)的流程,各種類型的拉動(dòng)系統(tǒng),均衡生產(chǎn)以及縮短工裝更換時(shí)間,生產(chǎn)周期被細(xì)分為增值時(shí)間和非增值時(shí)間?!?、開展持續(xù)改進(jìn)研討會(huì) 精益遠(yuǎn)景圖必須付諸實(shí)施,否則規(guī)劃得再巧妙的圖表也只是廢紙一張。實(shí)施***中包括什么(What),什么時(shí)候(When)和誰來負(fù)責(zé)(Who),并且在實(shí)施過程中設(shè)立評(píng)審節(jié)點(diǎn)。這樣,全體員工都參與到全員生產(chǎn)性維護(hù)系統(tǒng)中。在價(jià)值流程圖、精益遠(yuǎn)景圖的指導(dǎo)下,流程上的各個(gè)獨(dú)立的改善項(xiàng)目被賦予了新的意義,使員工十分明確實(shí)施該項(xiàng)目的意義。持續(xù)改進(jìn)生產(chǎn)流程的方法主要有以下幾種:消除質(zhì)量檢測(cè)環(huán)節(jié)和返工現(xiàn)象;消除零件不必要的移動(dòng);消滅庫(kù)存;合理安排生產(chǎn)***;減少生產(chǎn)準(zhǔn)備時(shí)間;消除停機(jī)時(shí)間;提高勞動(dòng)利用率?!?、營(yíng)造企業(yè)文化 雖然在車間現(xiàn)場(chǎng)發(fā)生的顯著改進(jìn),能引發(fā)隨后一系列企業(yè)文化變革,但是如果想當(dāng)然地認(rèn)為由于車間平面布置和生產(chǎn)操作方式上的改進(jìn),就能自動(dòng)建立和推進(jìn)積極的文化改變,這顯然是不現(xiàn)實(shí)的。文化的變革要比生產(chǎn)現(xiàn)場(chǎng)的改進(jìn)難度更大,兩者都是必須完成并且是相輔相成的。許多項(xiàng)目的實(shí)施經(jīng)驗(yàn)證明,項(xiàng)目成功的關(guān)鍵是公司領(lǐng)導(dǎo)要身體力行地把生產(chǎn)方式的改善和企業(yè)文化的演變結(jié)合起來?!鹘y(tǒng)企業(yè)向精益化生產(chǎn)方向轉(zhuǎn)變,不是單純地***用相應(yīng)的“看板”工具及先進(jìn)的生產(chǎn)管理技術(shù)就可以完成,而必須使全體員工的理念發(fā)生改變。精益化生產(chǎn)之所以產(chǎn)生于日本,而不是誕生在美國(guó),其原因也正因?yàn)閮蓢?guó)的企業(yè)文化有相當(dāng)大的不同。 5、推廣到整個(gè)企業(yè) 精益生產(chǎn)利用各種工業(yè)工程技術(shù)來消除浪費(fèi),著眼于整個(gè)生產(chǎn)流程,而不只是個(gè)別或幾個(gè)工序。所以,樣板線的成功要推廣到整個(gè)企業(yè),使操作工序縮短,推動(dòng)式生產(chǎn)系統(tǒng)被以顧客為導(dǎo)向的拉動(dòng)式生產(chǎn)系統(tǒng)所替代?!】偠灾?,精益生產(chǎn)是一個(gè)永無止境的精益求精的過程,它致力于改進(jìn)生產(chǎn)流程和流程中的每一道工序,盡最大可能消除價(jià)值鏈中一切不能增加價(jià)值的活動(dòng),提高勞動(dòng)利用率,消滅浪費(fèi),按照顧客訂單生產(chǎn)的同時(shí)也最大限度的降低庫(kù)存?!∮蓚鹘y(tǒng)企業(yè)向精益企業(yè)的轉(zhuǎn)變不可能一蹴而就,需要付出一定的代價(jià),并且有時(shí)候還可能出現(xiàn)意想不到的問題。但是,企業(yè)只要堅(jiān)定不移走精益之路,大多數(shù)在6個(gè)月內(nèi),有的甚至還不到3個(gè)月,就可以收回全部改造成本,并且享受精益生產(chǎn)帶來的好處。
戴爾的精益生產(chǎn)與豐田生產(chǎn)模式有哪些相同點(diǎn)與不同點(diǎn)
精益生產(chǎn)(Lean Production,簡(jiǎn)稱LP)是美國(guó)麻省理工學(xué)院數(shù)位國(guó)際汽車***組織(IMVP)的專家對(duì)日本豐田準(zhǔn)時(shí)化生產(chǎn)JIT(Just In Time)生產(chǎn)方式的贊譽(yù)稱呼。精益生產(chǎn)起源于20世紀(jì)50年代豐田汽車公司,而在80年代中期被歐美企業(yè)紛紛***用。
精益"準(zhǔn)時(shí)化"生產(chǎn)方式的概念,基本原則及特點(diǎn)是什么?
一些制造業(yè)界的朋友們常對(duì)精益生產(chǎn)與豐田生產(chǎn)系統(tǒng)(TPS),以及精益與6西格瑪-精益之間的關(guān)系感到困惑。謹(jǐn)以此文提出我個(gè)人就前一個(gè)題目的看法,與大家切磋。
精益是從豐田生產(chǎn)系統(tǒng)中研發(fā)出來的,其秉持的理念承襲了豐田系統(tǒng)的五大要素:尋找價(jià)值,認(rèn)識(shí)價(jià)值流,讓作業(yè)流動(dòng)起來,按客戶的需求拉動(dòng)生產(chǎn),持續(xù)改善。同時(shí)鼓勵(lì)找出問題,應(yīng)用PDCA的科學(xué)方法解決問題,并持續(xù)改進(jìn)。因此精益與TPS并沒有什么明顯的不同,精益生產(chǎn)所應(yīng)用的工具包括5S、看板、價(jià)值流、連續(xù)流、以及均衡生產(chǎn)等,也大多來自豐田。
有人會(huì)問,那為什么還要發(fā)展精益生產(chǎn)呢?Dr. James Womack和他的 MIT 團(tuán)隊(duì),在80年代探討全球汽車生產(chǎn)的研究項(xiàng)目時(shí),發(fā)現(xiàn)日本豐田汽車公司所***用的管理理念與方法與歐美其他公司有很大的不同。 因此用科學(xué)的分析方法將豐田公司的生產(chǎn)作業(yè)程序詳盡的記錄下來,出版了震驚世界的經(jīng)典之作 《改變世界的機(jī)器》 (“The Machine that Changed the World”)。他的目的是要把這套當(dāng)時(shí)連豐田自身都不一定有全面了解的作業(yè)方式介紹給世人,希望大家能認(rèn)真的學(xué)習(xí)。
雖然TPS是豐田公司的生產(chǎn)文化,著重點(diǎn)在汽車制造,但是這套方法可以廣泛的應(yīng)用在非汽車制造業(yè)。此外,許多豐田生產(chǎn)系統(tǒng)里沿用的方法,并不代表是豐田公司的專利,因?yàn)楹芏嗍菙?shù)百年來生產(chǎn)技術(shù)不斷改進(jìn)累集下來的經(jīng)驗(yàn)。每家公司都可以借鑒TPS,并開發(fā)出一套適用于自身企業(yè)文化的生產(chǎn)方法,今天全球的大公司包括GM、福特、德爾福、FAURECIA以及卡特匹勒等都有一套自己的生產(chǎn)系統(tǒng)。雖然其內(nèi)容多模仿TPS的方法,但沒有一家公司愿意用TPS這個(gè)名字來作為自己公司的管理系統(tǒng)與制造文化。
從另一個(gè)角度來看,早年亨利福特倡導(dǎo)用流水線生產(chǎn)汽車后,GM的Alfred Sloan將之發(fā)揚(yáng)光大,發(fā)展為一個(gè)可以制造不同車型以及多種顏色汽車的生產(chǎn)系統(tǒng)。這套生產(chǎn)方式在上一個(gè)世紀(jì)一直被視為全世界制造業(yè)的標(biāo)準(zhǔn)模式,世人稱之為大規(guī)模生產(chǎn)系統(tǒng)(Mass Production),并沒有人以福特或通用命名。同樣的道理,豐田汽車為了適應(yīng)50年代日本的特殊環(huán)境,改進(jìn)了大規(guī)模生產(chǎn)的體制,并整理出一套更符合今天市場(chǎng)需求的生產(chǎn)方法,用較少的***,較少的勞動(dòng)力,在較短的時(shí)間內(nèi),去完成同樣或更多的工作。因此Dr.Womack命名為L(zhǎng)ean Manufacturing.以與大規(guī)模生產(chǎn)方法區(qū)別,中國(guó)將之翻譯成精益生產(chǎn),臺(tái)灣將其翻譯成精實(shí)生產(chǎn)。
有人比喻TPS是日本式的生產(chǎn)系統(tǒng),而精益是西方式的改良制造方法,究其不同實(shí)在極乎其微。精益生產(chǎn)已被西方學(xué)者記錄寫成出工具書,許多不同國(guó)家的企業(yè)都已學(xué)習(xí)并實(shí)施,因此使用的人比較多。豐田汽車承襲了戴明教授的PDCA科學(xué)方法,融入超市與及時(shí)補(bǔ)貨的供料方法,將福特的汽車生產(chǎn)技術(shù)發(fā)揚(yáng)光大,誠(chéng)屬難得,但想學(xué)的人往往不得其門而入。Dr.Womack將豐田的生產(chǎn)方法記述下來供大家參考,希望大家能學(xué)習(xí)這套以最小的投入換取最大的利潤(rùn)的管理方法。兩者是同一付藥,不同的包裝。
1、精益"準(zhǔn)時(shí)化"生產(chǎn)方式的概念
準(zhǔn)時(shí)生產(chǎn),又譯實(shí)時(shí)生產(chǎn)系統(tǒng),簡(jiǎn)稱JIT系統(tǒng),在1953年由日本豐田公司的副總裁大野耐一提出,是由日本豐田汽車公司創(chuàng)立的一種獨(dú)特的生產(chǎn)方式。指企業(yè)生產(chǎn)系統(tǒng)的各個(gè)環(huán)節(jié)、工序只在需要的時(shí)候,按需要的量,生產(chǎn)出所需要的產(chǎn)品。
2、精益"準(zhǔn)時(shí)化"生產(chǎn)方式的原則
應(yīng)使產(chǎn)品的設(shè)計(jì)與市場(chǎng)需求一致。應(yīng)考慮出便于生產(chǎn)的產(chǎn)品設(shè)計(jì)。應(yīng)盡量***用成組技術(shù)和流程式生產(chǎn)。應(yīng)與原材料或外購(gòu)件的供應(yīng)者建立聯(lián)系,為JIT 供應(yīng)原材料。
3、精益"準(zhǔn)時(shí)化"生產(chǎn)方式的特點(diǎn)
追求現(xiàn)場(chǎng)管理的整體優(yōu)化,各種管理方法、手段都緊緊圍繞提高產(chǎn)品質(zhì)量,提高經(jīng)濟(jì)效益而配套設(shè)計(jì),同步實(shí)施。
同時(shí)改變過去上道工序推動(dòng)下道工序的“推動(dòng)式”生產(chǎn),為后工序需要多少,前工序就生產(chǎn)供應(yīng)多少的“拉動(dòng)式”生產(chǎn),企業(yè)以市場(chǎng)的需求為目標(biāo)組織準(zhǔn)時(shí)化生產(chǎn)。最大限度地壓縮在制品儲(chǔ)備,杜絕超量生產(chǎn),工序間在制品向“零”進(jìn)軍,從而能保證產(chǎn)品質(zhì)量,避免成批廢品的產(chǎn)生。
在勞動(dòng)組織上實(shí)行多工序管理,多機(jī)床操作,使勞動(dòng)生產(chǎn)率大幅度提高。在現(xiàn)場(chǎng)管理上,強(qiáng)調(diào)更新觀念,實(shí)行以生產(chǎn)現(xiàn)場(chǎng)為中心,以生產(chǎn)工人為主體,以車間主任為首的生產(chǎn)現(xiàn)場(chǎng)管理體制,要求一切后方部門都必須圍繞準(zhǔn)時(shí)化生產(chǎn)提供優(yōu)質(zhì)準(zhǔn)時(shí)的服務(wù),保證生產(chǎn)工人分分秒秒不停地創(chuàng)造附加價(jià)值。
擴(kuò)展資料
準(zhǔn)時(shí)化生產(chǎn)是一種“拉動(dòng)”式生產(chǎn)管理模式,看板系統(tǒng)是準(zhǔn)時(shí)化生產(chǎn)的重要工具之一。準(zhǔn)時(shí)化生產(chǎn)方式通過看板管理,成功地制止了過量生產(chǎn),實(shí)現(xiàn)了“在必要的時(shí)刻生產(chǎn)必要數(shù)量的必要產(chǎn)品(或零配件)”,從而徹底消除在制品過量的浪費(fèi),以及由之衍生出來的種種間接浪費(fèi)。
然后通過旨在解決這些問題的改善活動(dòng),徹底消除引起成本增加的種種浪費(fèi),實(shí)現(xiàn)生產(chǎn)過程的合理性、高效性和靈活性??窗逑到y(tǒng)也是JIT生產(chǎn)現(xiàn)場(chǎng)控制技術(shù)的核心。利用看板技術(shù)控制生產(chǎn)和物流,以達(dá)到準(zhǔn)時(shí)生產(chǎn)的目的。
從本質(zhì)上講,JIT生產(chǎn)方式是一種生產(chǎn)管理技術(shù)。但就JIT生產(chǎn)方式的基本理念來說,“準(zhǔn)時(shí)化”不僅僅限于生產(chǎn)過程的管理。
“準(zhǔn)時(shí)化”是一種現(xiàn)代經(jīng)營(yíng)觀念和先進(jìn)的生產(chǎn)組織原則,它所追求的是生產(chǎn)經(jīng)營(yíng)全過程的合理性、高效性和靈活性。它是包括經(jīng)營(yíng)理念、生產(chǎn)組織、物流控制、質(zhì)量管理、成本控制、庫(kù)存管理、現(xiàn)場(chǎng)管理和現(xiàn)場(chǎng)改善等在內(nèi)的完整的生產(chǎn)管理技術(shù)與方法體系。
準(zhǔn)時(shí)化生產(chǎn)JIT是二戰(zhàn)以后最重要的生產(chǎn)方式之一。由于它起源于日本的豐田汽車公司,因而曾被稱為“豐田生產(chǎn)方式”,后來隨著這種生產(chǎn)方式的獨(dú)特性和有效性,被越來越廣泛地認(rèn)識(shí)、研究和應(yīng)用,人們才稱為JIT。
參考資料的來源:百度百科——準(zhǔn)時(shí)化生產(chǎn)方式
標(biāo)簽: #生產(chǎn)